Shopping Bags
“Would you like paper or plastic today?”
“I brought my own – thank you”
How do you know what bag to choose? Paper or plastic? Woven or non-woven reusable? Every bag has its pros and cons towards the environment and all should be properly examined to pick your next bag choice. Each type of bag is uniquely made from different materials and we cannot generalize their environmental impact. There are two general types of bags, single use and multi-use, that we will be discussing (Muthu, 2015).
Plastic bags:
While plastic bags are convenient for most shoppers, the cons outweigh the pros by far. 80% of grocery and convenience stores contain plastic bags for shoppers (Muthu & Li, 2012). Most plastic shopping bags are destined to end up in landfills (Muthu, 2015), and the ones that don’t litter the ocean. In America alone, it’s found that over 380 billion plastic bags, sacks, and wraps are consumed yearly (Northern, 2012) comparing to the 6.9 billion bags are consumed each year in Australia. Of the 69 in Australia, 30 million litter the environment (James & Grant, 2005). They are created from non-renewable sources such as petroleum and natural gasses (Muthu, 2011) and along with that, they are non-biodegradable (Muthu, 2015). Plastic is a by-product of the oil refining process and of the oil used in plastic bag manufacturing, makes up 4% of the world’s total oil production (Muthu, 2014). The ones you find at grocery stores are usually made of linear low-density polyethylene which helps achieve the desired thickness and high glossiness in the bags (Muthu et al., 2011). They extract the polyethylene with an oil cracking process followed by other processes. The bags contain additives to prevent the layers from sticking, a slip to allow the bag to open with ease, and an Ultra Violet Inhibitor to prevent UV rays from damaging the quality. All the elements are then melted down and blown into a mold. After the parts of the bags are created, a machine heat seals one end of the product. Of these processes described, energy and natural resources are used extensively (Muthu, 2014).
The bags have a short lifespan by being a single-use bag (Muthu, 2015); they’re created to be used and recycled but many just end up garbage cans. Using simple math, the average person can calculate the carbon footprint of their plastic bag usage. As the carbon footprint of plastic is about 6kg CO2 per kilogram of plastic, multiplying the weight of your plastic bags by how many bags you use per year will determine approximately how much carbon dioxide is emitted into the air. It is found that for five plastic bags, 1kg of CO2 was created (Juerg, 2009).
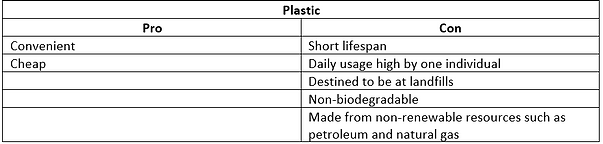
Paper:
Unlike the plastic counterpart, paper bags are created with renewable resource – pulpwood (Muthu et al., 2011). Pulpwood can be made from both hardwoods and softwoods such as spruce and fir or poplar and elm. The felled trees then must be processed into pulp which is through either a mechanical [fuel and energy] or a chemical process. Within the mechanical process, the wood is forced through grinders to break it down which then dumps it into a filter to gather the pulp and leave out foreign objects (Advameg, 2017). The grinding process physically separates the cellulose fibers which then the mill will wash [water usage] (EPA). During the chemical process, a chemical bath of sodium hydroxide and sodium sulfide which removes the bark. This would also be the stage that bleach or dyes could be added. Most of paper bags we see at stores are brown which could mean they skip this step. The broken-down pulp is then transported to paper plants, which means fuel is burned (Advameg, 2017). The pulp is put through a beating process to press it down to size the paper. Sizing effects the way the paper will react to ink – whether that be pen ink or ink to create designs on the bags. From there, paper is made using a Fourdrinier machine. It contains a moving belt that forces the pulp through a fine mesh screen, which makes them fall into a set of rollers with a suction device to drain the water. The paper then goes into a press where it is pressed between wool felt rollers and then steam-heated cylinders to remove the remaining water. A large machine typically holds 40 to 70 drying cylinders which uses water to create constant steam (Advameg, 2017). This whole process uses constant energy along with lots of water.
The last step of paper making is putting it into large rolls for it to be shipped off for its ultimate use, in this case, paper shopping bags. It will be shaped and dyed appropriately and then folded, glued, and handles will be attached if necessary (Muthu, 2014).
While paper bags can be recycled to be broken back down and made into other paper products, there are environmental concerns that come with the creation of the simple-seeming bags. The paper companies claim that they plant a tree for every tree they chop down, but environmentalists argue that the new trees cannot replace the old ones as they are much smaller. The dyes, ink, and sizing chemicals are also harmful to the environment as they are often released into water and nearby land after they’re used. However, there are now federal requirements for pollution-free paper production (Advameg, 2017)
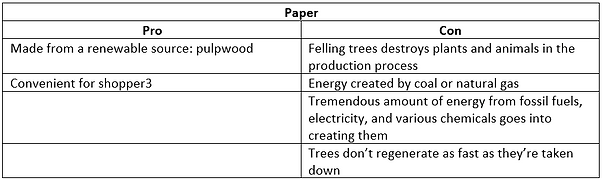
Woven, cotton, reusable:
The cotton reusable bags are a better choice when it comes to the lifespan on the product, but it does create pollution in the manufacturing process. Every step of creating cotton to weaving the bags has to be accounted for when considering a woven cotton bag. I will be discussing the typical process that Life Cycle assessment of Cotton Fiber & Fabric talks about, but every company may not go through ever step. There are also organic cotton bags offered which would be the better route to take of the two.
During the agricultural phase, it’s difficult to calculate everything that happens as it depends on the area the cotton is grown. Every farm has different soils, irrigation systems (which leads to different energy usage), fertilizers, and weather. However, when considering the model, they took account of nitrogen emissions such as nitrate (NO3-) in water and nitrous oxide (N2O), nitrogen oxide (NO) and ammonia (NH3) into the air along with carbon emissions such as methane (CH4), carbon monoxide (CO) and carbon dioxide (CO2). These carbon emissions are a result of fertilizer production, pesticide use, electricity, and diesel use in tractors or irrigation engines (The Cotton Foundation, 2012).
In the bale to weaving process, energy is the major input while natural gas is also used. There are also many wastes such as plant bark and fiber waste, you can refer to figure 37 on page 85 of the assessment for the entire concept map. In the weaving to finished product stages of the bags life cycle, chemicals such as bleach, dyes, wrinkle resist, soil replant, water resist, and softener can be added. Just within the continuous dyeing stage, chemicals, dyes, electricity, natural gas, and steam goes into singeing, desizing, scouring, bleaching, mercerizing, dying, and drying, this map is located on page 86 of the assessment. Water is used in many of these stages as well; dying with chemicals leads to emissions to water and wastewater treatment processes that relate back to singeing (The Cotton Foundation, 2012).
The use stage is where the cotton bags strive. They are built durably and will last hundreds of shopping trips. With the high reuse rate, it keeps the bags out of the landfill and off the streets as litter. With this stage lasting as long as it does, it could potentially balance the overall impacts of the entire life cycle (Muthu, 2015). In theory, not as many of these bags will have to be produced. If everyone replaced their seven, single-use, plastic bags with three reusable cotton bags, everyone’s carbon footprint could be lowered drastically.
The disposal of these bags can lead to creating recycled cotton bags (or other cotton products) which saves these from hitting landfills or trashing the streets. With a longer process, they take longer to produce, but potentially cuts down on CO2 emissions overall.
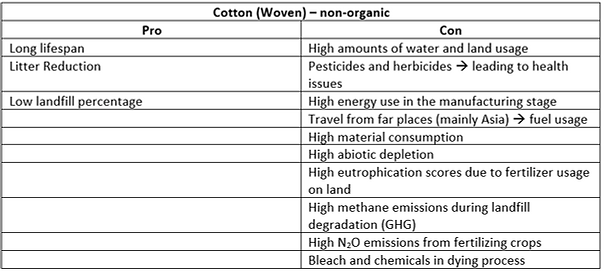
Non-woven reusable:
There is little information on non-woven reusable bags available. However, this is what was found.
These reusable bags are usually made out of polypropylene (Muthu et al., 2011) – a substance that makes up many everyday plastic objects such as the chairs you sit on in classrooms. It is found that these bags are better in terms of their carbon footprint when comparing it to its counterparts of paper or plastic (Edwards & Fry, 2011).
When it comes to reusable bags, they usually fit more items compared to the basic plastic bags and you can use them repeatedly. When going to the store, instead of using 5 plastic bags, you could use 3 reusable bags and the same bags the next week for the next shopping trip.

What We Use
Any reusable bag is better than a single-use based off of the life of the product alone. With them being reused, they won’t be as mass produced meaning the H2O inputs and CO2 outputs won’t be as drastic compared to the counterparts (Juerg, 2009).
References
Advameg. (2017). Paper. Retrieved November 21, 2017, from http://www.madehow.com/Volume- 2/Paper.html
The Cotton Foundation. (2012). Life Cycle Assessment of Cotton Fiber & Fabric (pp. 7-123, Rep.). Cotton Incorporated.
Edwards, C., Dr., & Fry, J. M. (2011). Life cycle assessment of supermarket carrier bags: a review of the bags available in 2006 (Rep. No. SC030148). Bristol: Environment Agency.
EPA. "Paper Making and Recycling." U.S Environmental Protection Agency. Accessed November 21, 2017. https://archive.epa.gov/wastes/conserve/materials/paper/web/html/papermaking.html.
James, K., & Grant, T. (2005). LCA of Degradable Plastic Bags (pp. 1-16, Rep.). Centre for design at RMIT University.
Juerg. (2009). Plastic bags and plastic bottles - CO2 emissions during their lifetime. Retrieved November 19, 2017, from http://timeforchange.org/plastic-bags-and-plastic-bottles-CO2-emissions
Muthu, S. S., Li, Y., Hu, J., & Mok, P. (2011). Carbon footprint of shopping (grocery) bags in China, Hong Kong and India. Atmospheric Environment, 45(2), 469-475. doi:10.1016/j.atmosenv.2010.09.054
Muthu, S. S., & Li, Y. (2012). Eco-Impact of Plastic and Paper Shopping Bags. Journal of Engineered Fibers and Fabrics, 7(1), 26-36.
Muthu, S. S. (2015). LCA of cotton shopping bags. Handbook of Life Cycle Assessment, 283-299.
Muthu, S. S. (2014). Manufacturing Process of Grocery Shopping Bags. Assessment of Environmental Impact by Grocery Shopping Bags: an Eco-functional Approach, 7-14. Retrieved November 20, 2017.
Northern Michigan Environmental Action Council (Ed.). (2012). Many facts...one conclusion (reuse). Retrieved November 30, 2017, from http://www.nmeac.org/Toolkit/Plastic/facts.html